Vinyl pressing UK | One off vinyl pressing | Vinyl guides
Vinyl pressing UK - Guides, How to's & help tutorials
manufacture?Audio formats
& side lengthsAudio mixing
tips for vinylWhy have
test-pressings?Sleeves, labels
& insertsAbbey Road
lacquer cutsHeavyweight, colour
& picture vinylWhat are
download codes?How are
records made?
Fast turnarounds to suit your deadlines
Standard
turnaround
Test-pressings: 4 weeks
Main-pressings: 4 weeks
Express
turnaround
Test-pressings: 2.5 weeks
Main-pressings: 2.5 weeks
Super express turnaround
Test-pressings: 6 to 10 days
Main-pressings: 6 to 10 days
How much audio can fit on a vinyl record?
7" vinyl
33 rpm:
Optimal: 5 mins per side
Maximum: 7 mins per side
(We don't recommend 33 rpm for 7" vinyl)
45 rpm:
Optimal: 4 mins per side
Maximum: 5 mins per side
10" vinyl
33 rpm:
Optimal: 9 mins per side
Maximum: 14 mins per side
45 rpm:
Optimal: 8 mins per side
Maximum: 11 mins per side
12" vinyl
33 rpm:
Optimal: 20 mins per side
Maximum: 24 mins per side
45 rpm:
Optimal: 12 mins per side
Maximum: 15 mins per side
Side lengths & cutting speed
The above times should be used as a guide. Bass heavy music means wider grooves, and shorter side lengths, and the converse for music not so heavy on the low frequencies.
Audio supplied at maximum side lengths means we may need to cut the audio at a lower volume level in order for all the audio to fit on the side. This could result in the vinyl being up to 6db lower in volume compared to a cut at optimal lengths. This audio level reduction depends on the frequency range of the music.
Bass heavy music means deeper and wider grooves, which result in either shorter audio lengths per side, or lower audio levels for longer sides to fit.
In comparison, solo classical guitar frequency range is likely to have less bass than dance music, and as a result, a side of 25mins of classical guitar will not be reduced too much in level compared to optimal.
33 rpm versus 45 rpm
Whilst audio cut at 33rpm produces a great sound on 12” and 10” records, 45rpm cuts result in even better audio fidelity.
For 7” we strongly advise against 33rpm cuts as they tend to result in a degraded audio quality.
How to prepare your audio files
Supply continuous audio files
Prepare a single continuous stereo audio file of your tracks in the correct order for each side of the record. These files should include appropriate gaps between the track (normally about 3 to 4 seconds).
We will not alter this audio in any way, and the lacquer will be cut directly from the supplied continuous files.
Along with the audio files, provide a list of Visual Track Marker points (known as VTMs for short). These are the points at which the lacquer and records will be marked to indicate the start of a track, and make it easier for the listener to skip to the start of a particular song on the record.
For example, if your Side A continuous file consists of 4 tracks with the following lengths; 1.30min / 4 sec gap / 2.45 / 4 sec gap / 3.30 / 4 sec gap / 2.30, then the VTM list should read as follows:
Provide individual tracks
We can accept individual song files and tracks. We’ll set up and create the continuous audio files and VTM points.
The new audio files will be emailed back to check and approve. There is a cost of £35+vat for the service.
Audio mixing tips for vinyl records
A well mixed track following good mixing practices should also translate well to vinyl, there are however some key points to check for before sending your audio for vinyl manufacture.
View our full guide on preparing your mixes for vinyl manufacture.
Control high frequencies
Bass & low frequencies
Remove sibilance
Apply a ‘de-esser’ to vocals to remove excessive sibilance.
Stereo panning
Compression & loudness
Track ordering
Why make test-pressings?
Test-pressings are the first records made from the pressing plates and offer the first opportunity to evaluate the quality of the audio before the main pressing takes place.
Most test-pressings are approved first time, however a test-pressing could contain a jump or loud pop, which requires fixing before the main pressing takes place.
What if I choose not to have test-pressings?
Test-pressings are recommended to ensure that the vinyl are free from any excessive pops, skips and other unwanted noise. Due to time constraints, some customers choose not to have any test-pressings, and opt straight for the main manufacture.
We do check a random pressed record as they are coming off the press to check for any obvious issues. However, incase something is not picked up in our checks, then any rework is additionally billable.
Test-pressings are supplied with a white label and packed into a white inner.
Centre labels, inners sleeves & outer vinyl cases
Centre vinyl record labels
Inner sleeve packaging
Outer vinyl packaging
All master lacquers cut at Abbey Road Studios
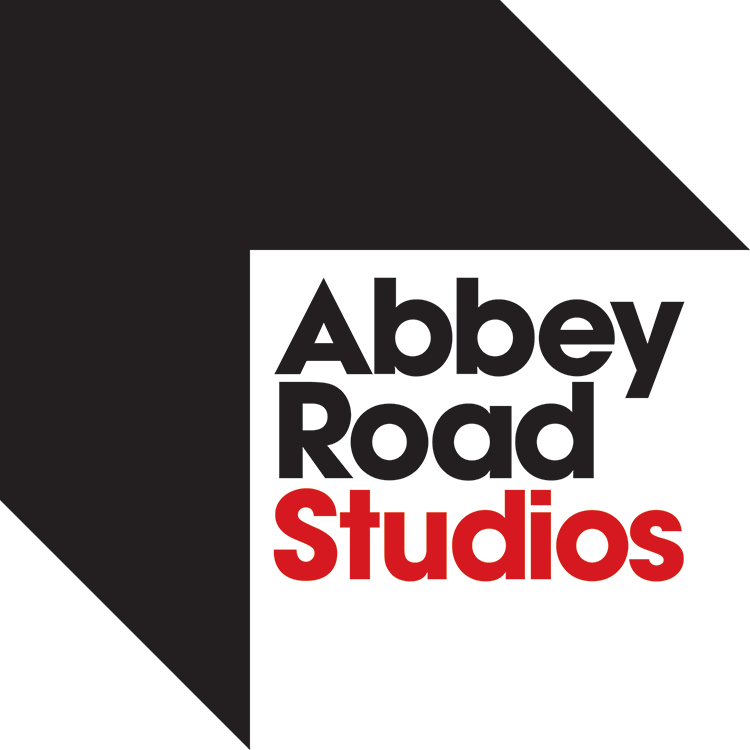
Your music cut by award winning engineers
All our master lacquers are cut Abbey Road studios by award winning engineers to ensure your music sounds it’s absolute best when pressed to vinyl.
Our lacquers are cut on VMS80 Neuman lathes and the Abbey Road engineers will make tweaks and adjustments to your music to ensure the music sounds it’s very best and totally awesome once cut to vinyl.
100% test-pressing approval rate
We are proud to say all our masters cut at Abbey Road have had a 100% first test-pressing approval rate till now.
This fantastic reliably ensures your deadlines are met and your finished vinyl records are delivered as soon as possible and bang on time.
Attend your lacquer cutting at Abbey Road Studios
You can attend and watch and witness your music being cut onto the vinyl lacquer master live and in person. Speak to us for more information.
Heavyweight vinyl, colour vinyl & picture vinyl pressing
Heavyweight vinyl pressing
Colour vinyl pressing
White
ID: OM0001
Bright White
ID: OM0005
Polar White
ID: OM0330
Coconut
ID: OM0332
Magnolia
ID: OM1275
Vanilla
ID: OM1293
Sunflower Yellow
ID: OM1625
Daffodil Yellow
ID: OM1637
Citrus
ID: OM1690
Banana
ID: OM1693
Jasmine
ID: OM1696
Canary Yellow
ID: OM1700
Marigold
ID: OM1702
Ivory
ID: OM1704
Cream
ID: OM1707
Sol Yellow
ID: OM1751
Sherbert Lemon
ID: OM1753
Linen
ID: OM1831
Buttermilk
ID: OM1832
Chick
ID: OM1834
Custard
ID: OM1839
Yolk
ID: OM1845
Seville Orange
ID: OM2239
Mandarin Orange
ID: OM2243
Pumpkin
ID: OM2250
Nectarine
ID: OM2252
Carrot
ID: OM2291
Strawberry Red
ID: OM3223
Rose Pink
ID: OM3364
Flesh Pink
ID: OM3513
Cherry Red
ID: OM3788
Pastel Pink
ID: OM3801
Flame Red
ID: OM3820
Lobster Red
ID: OM3849
Tomato Red
ID: OM3850
Fuchsia
ID: OM3853
Admiral Red
ID: OM3856
Cardinal Red
ID: OM3861
Fire Engine Red
ID: OM3864
Rocket Red
ID: OM3872
Raspberry
ID: OM3879
Brilliant Red
ID: OM3947
Poppy Red
ID: OM3951
Valentine Red
ID: OM3955
Bubblegum Pink
ID: OM3958
Ruby
ID: OM33053
Burgundy
ID: OM4043
Mulberry
ID: OM4204
Aubergine
ID: OM4211
Cerise
ID: OM4219
Sky Blue
ID: OM5001
Powder Blue
ID: OM5009
Mid Blue
ID: OM5011
Royal Blue
ID: OM5027
Pale Blue
ID: OM5034
Navy Blue
ID: OM5065
Ultra Blue
ID: OM5179
Pacific Blue
ID: OM5485
Baby Blue
ID: OM5982
Purple
ID: OM55094
Ice Blue
ID: OM55157
Midnight Blue
ID: OM55160
Cornflower Blue
ID: OM55162
Baltic Blue
ID: OM55171
African Violet
ID: OM55302
Mistral
ID: OM55484
Lavender
ID: OM55497
Bluebell
ID: OM55500
Lilac
ID: OM55502
Aqua
ID: OM6037
Alpine Green
ID: OM6969
Spearmint Green
ID: OM6985
Leaf Green
ID: OM6994
Fern Green
ID: OM66070
Springtime
ID: OM66072
Racing Green
ID: OM66075
Fresh Green
ID: OM66083
Sage Green
ID: OM66087
Marine Blue
ID: OM66088
Lime Green
ID: OM66099
Olive Green
ID: OM66100
Pod Green
ID: OM66159
Ocean Green
ID: OM66161
Dewdrop
ID: OM66301
Grass Green
ID: OM66303
Lettuce Green
ID: OM66306
Apple Green
ID: OM66307
Light Grey
ID: OM7002
Dark Grey
ID: OM7020
Ash Grey
ID: OM7021
Mid Grey
ID: OM7053
Dove Grey
ID: OM7378
Soft Grey
ID: OM7759
Graphite
ID: OM7994
Moonstone
ID: OM7996
Pebble
ID: OM7999
Cloud Grey
ID: OM77000
Mink
ID: OM77007
Dusk
ID: OM77013
Putty
ID: OM77140
Storm Grey
ID: OM77142
Vapour
ID: OM77326
Pigeon
ID: OM77327
Shark
ID: OM77330
Chocolate Brown
ID: OM8004
Terracotta
ID: OM8005
Light Brown
ID: OM8018
Mushroom
ID: OM8021
Mid Brown
ID: OM8029
Dark Brown
ID: OM8142
Mahogany
ID: OM8332
Rosewood
ID: OM8399
Toffee
ID: OM88721
Honey Beige
ID: OM88723
Chestnut Brown
ID: OM88726
Beige
ID: OM88729
Fudge
ID: OM88820
Demerara
ID: OM88833
Sandstone
ID: OM88942
Deep Black
ID: OM0055
Ebony
ID: OM0086
Onyx
ID: OM0093
Picture vinyl pressing
Add digital download codes to your vinyl release!
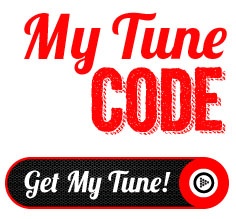
How are vinyl records made?
Stage 1
Lacquer cutting
Stage 2
Galvanics
Stage 3
Pressing plates
Stage 4
Test-pressings
Stage 5
Main-pressings
Stage 6
Packaging
12" vinyl pressing
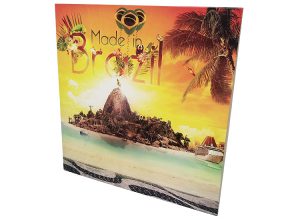
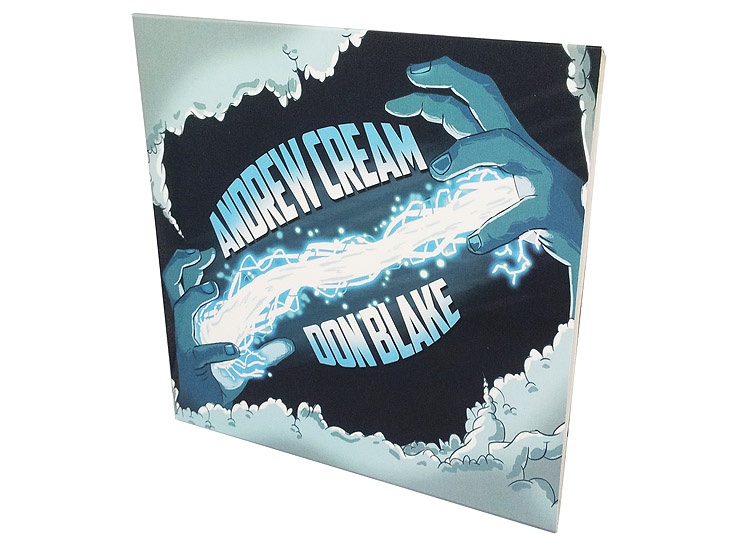
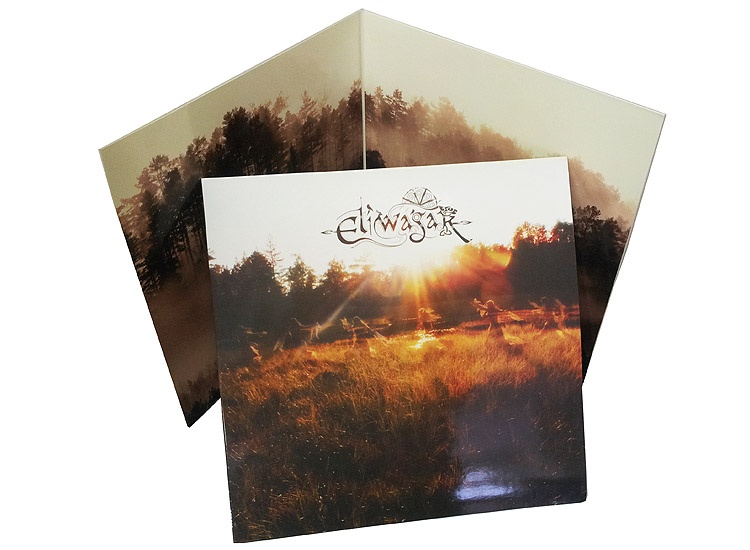
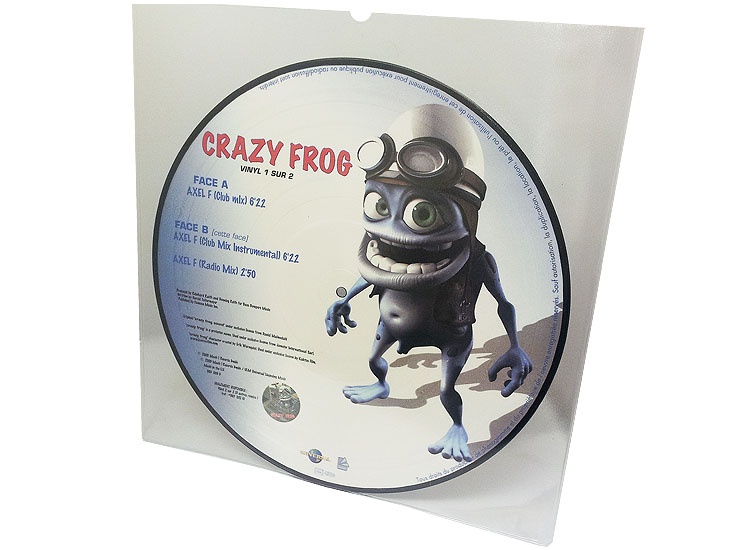
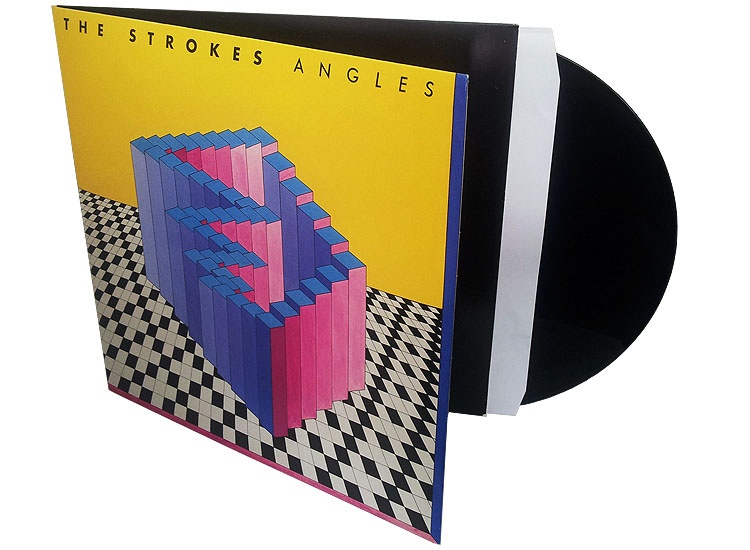
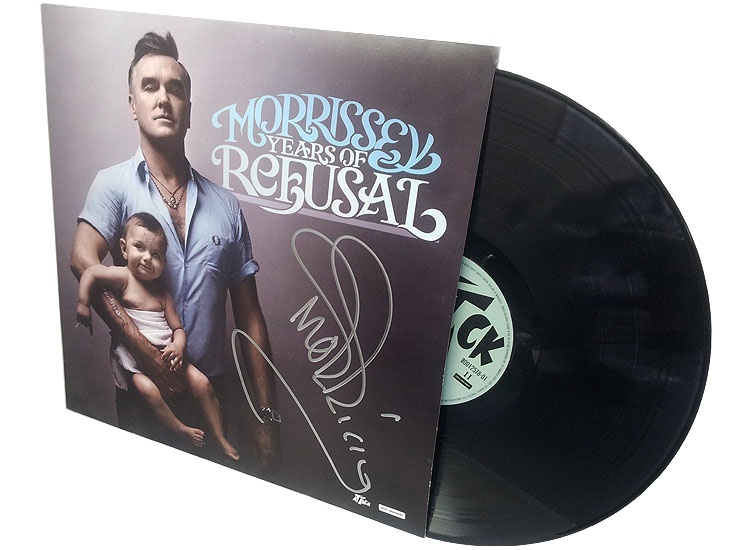
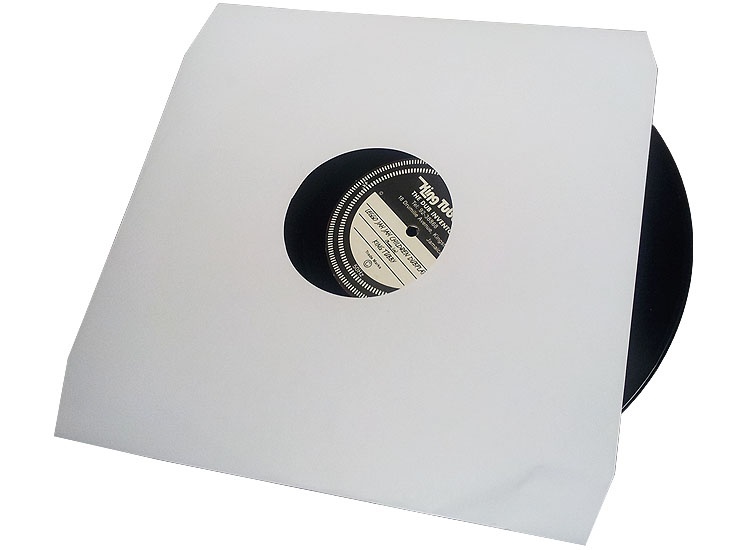
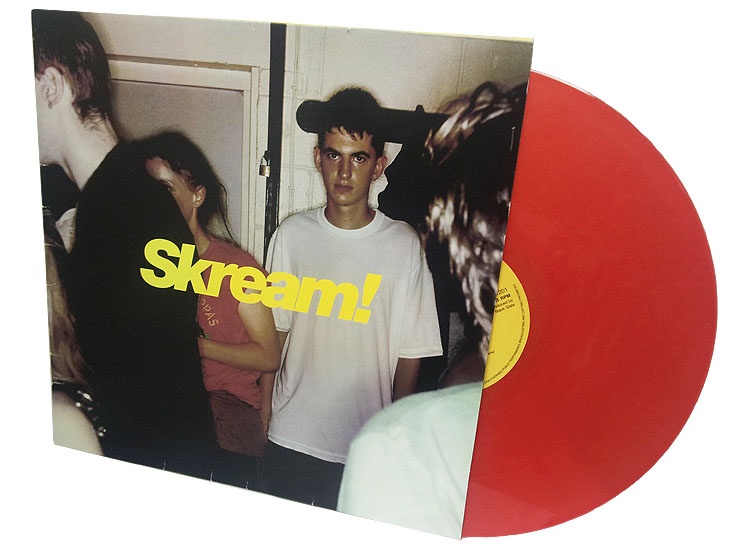
12" vinyl features & add-ons
On a standard turnaround we aim to have test-pressings ready within 4 weeks. Once approved, main pressing takes a further 4 weeks.
Express turnaround means test-pressings ready in approx 2.5 weeks, and on approval, main pressing ready in a further 2.5 weeks.
Test-pressings ready within 7 to 10 days, and on approval, main pressings ready in another 7 to 10 days.
Upgrade to heavyweight (180 gram) vinyl or have a colour pressing. Heavyweight and colour pressing can also be combined. View available vinyl colours.
All prices include white inner paper sleeves. Add-ons available black & poly lined inners or custom printed inners sleeves. Printed 2 sided inserts also available.
All outer sleeve packaging is printed on heavyweight art board and with the option of gloss or matt finish included. Uncoated and reverse board print available.
We can print and insert download cards with unique, one time use codes. This lets customers download a digital version of the album.
All vinyls master lacquers are cut at Abbey Road Studios. This ensures your music sounds the best it possibly can when pressed to vinyl records.
Free overnight and tracked UK delivery is included with all orders. We also deliver world-wide with fast and reliable courier services.
12 inch vinyl templates
7" vinyl pressing
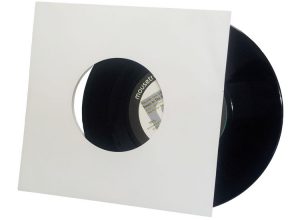
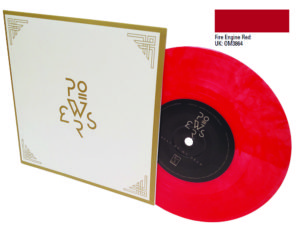
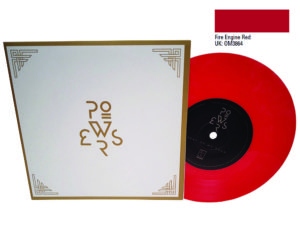
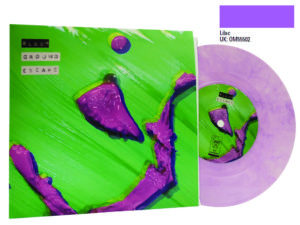
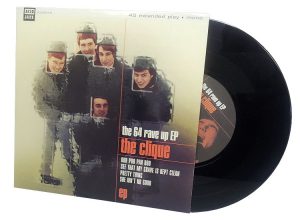
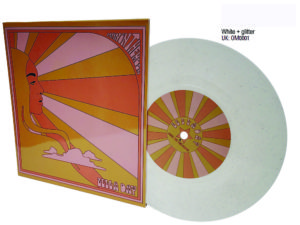
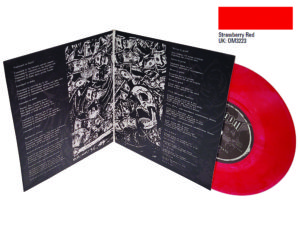
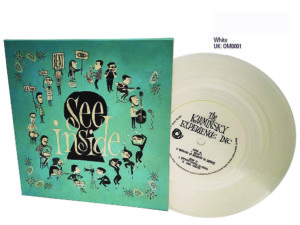
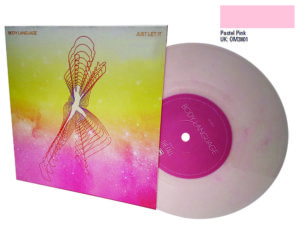
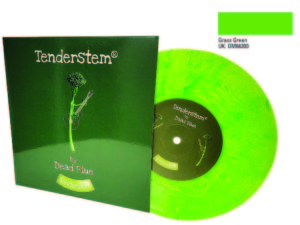
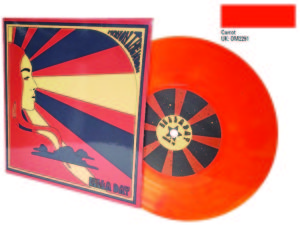
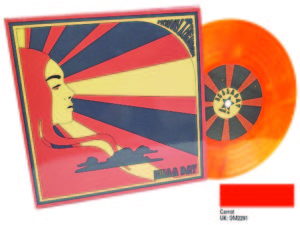
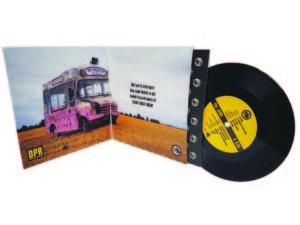
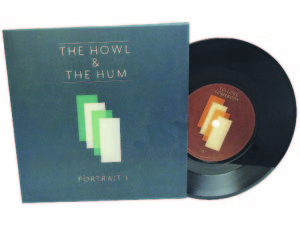
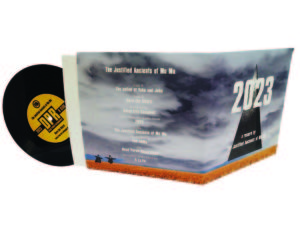
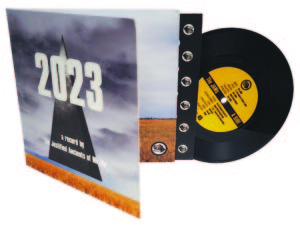

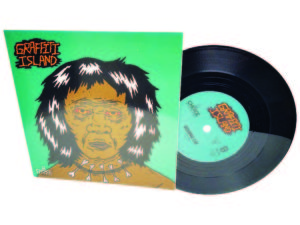
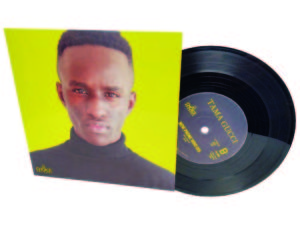

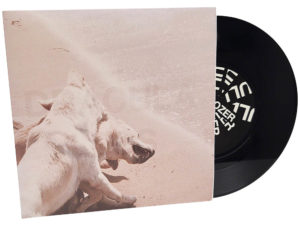
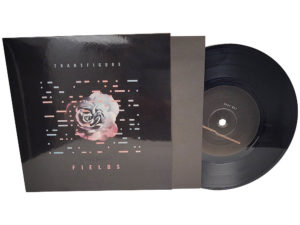
7" vinyl features & add-ons
On a standard turnaround we aim to have test-pressings ready in 4 weeks. Once approved, The main pressing takes a further 4 weeks.
Express turnaround means test-pressings ready in approx 2.5 weeks, and on approval, main pressing ready in a further 2.5 weeks.
Test-pressings ready within 7 to 10 days, and on approval, main pressings ready in another 7 to 10 days.
We offer a huge range of colours for 7" vinyl. View available vinyl colours. 7" picture disc pressing avaiable too.
All prices include white inner paper sleeves. Add-ons available black & poly lined inners or custom printed inners sleeves. Printed 2 sided inserts also available.
All outer sleeve packaging is printed on heavyweight art board and with the option of gloss or matt finish included. Uncoated and reverse board print available.
We can print and insert download cards with unique, one time use codes. This lets customers download a digital version of the album.
All vinyls master lacquers are cut at Abbey Road Studios. This ensures your music sounds the best it possibly can when pressed to vinyl records.
Free overnight and tracked UK delivery is included with all orders. We also deliver world-wide with fast and reliable courier services.
7 inch vinyl templates
One off vinyl cuts - 12" & 7"
Disc Wizards offer one or a handful of one off cuts of your music onto vinyl record. Each record is individually hand cut,and is supplied with a printed centre label sticker, in white paper inners and white or black outer card sleeves.
20 mins of audio each side
We can cut upto 20 mins on each side of the record. That's a total of 40 mins of audio over both sides cut at 33 rpm.
White or black inner & outer sleeves
Each record is individually packed into paper inner sleeves, and plain white or black outer card sleeves.
Printed centre labels
All one-off cuts are supplied with printed centre labels with custom printed graphics. Just supply the artwork design.
Clear & white vinyl options
Black vinyls are included in the costs. However for an additional fee we can cut the music on clear or white colour vinyl.
12" one off cut prices
7" one off cut prices
4m 30s per side
7" vinyl can hold 4 mins 30 secs each side at 45 rpm. That's 9 mins of audio in all.
White or black sleeves
7" cuts are supplied with paper inner sleeves, and plain white or black outer card sleeves.
Printed centre labels
Printed centre labels with print are included in the costs. Artwork to be supplied on our tempaltes.
Clear & white vinyl options
Black vinyl as standard. White and clear vinyl cuts also available.